Confronting Our Planet’s Polymer Problem
Northwestern researchers seek solutions to the plastics pollution dilemma with new ideas on polymer design and upcycling.
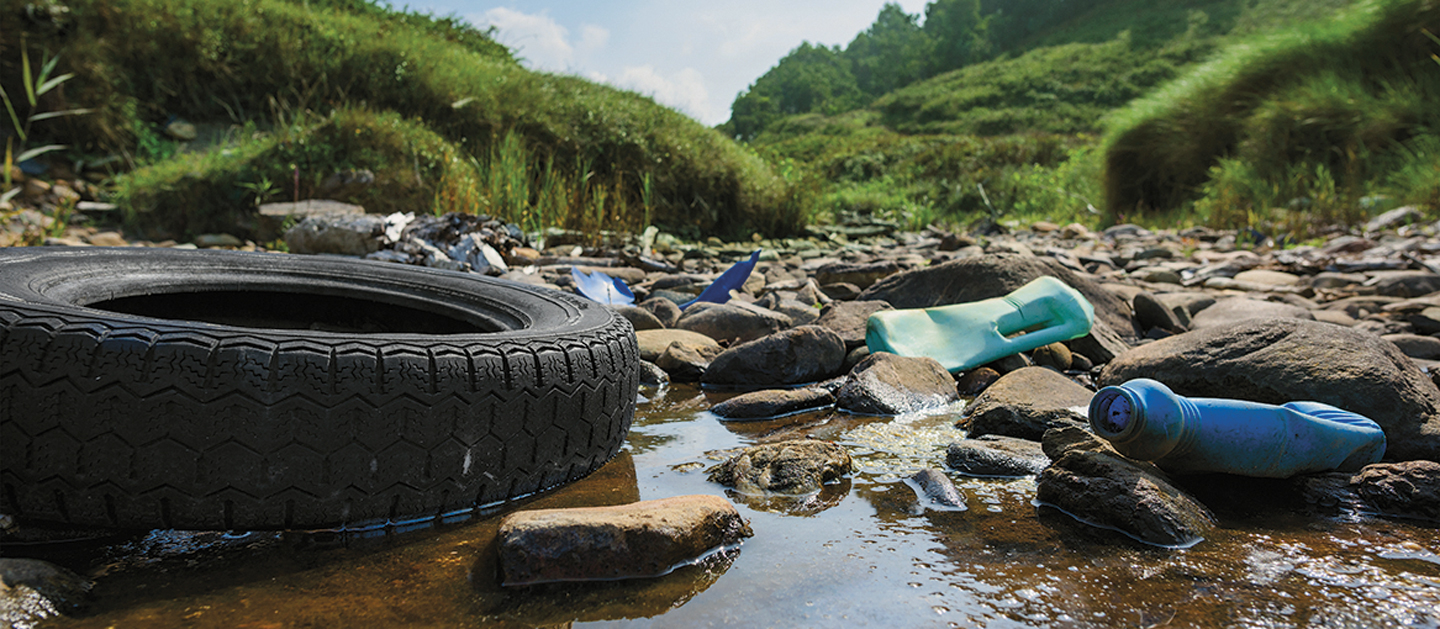
Many polymers—including plastics used to manufacture the plethora of products used only once and thrown away—don’t degrade easily and consequently pack our landfills and pollute our waterways.
The statistics are dismal. Something as simple and ubiquitous as a plastic shopping bag can take 1,000 years to decompose. Researchers find tiny pieces of these materials in fish, table salt, human organs, and even breast milk.
Though not every polymer ends up in the environment, the prospect of reusing these materials remains dim. At best, less than 10 percent of plastics are recycled.
Still, there is reason for hope: Northwestern Engineering professors are working to quantify just how much of these materials plague our environment and, at the same time, are developing new polymer designs and upcycling processes to help ensure a cleaner, greener future.
Taking on Microplastic Pollution
Experts say that microplastics—small plastic pieces less than five millimeters long—linger in rivers for years before entering the world’s oceans, which are estimated to contain millions of tons of them. It’s a global pollution problem that scientists worldwide are studying.
Because rivers are in near-constant motion, researchers previously assumed lightweight microplastics quickly flowed through them, rarely interacting with riverbed sediments. To the contrary, a team led by the McCormick School of Engineering and the University of Birmingham in England has found that these plastics can deposit and linger within riverbeds for as long as seven years before washing into the ocean.
These deposited microplastics cause ecological damage, and the large amount of deposited particles means that it will take a very long time for all of them to be washed out of our freshwater ecosystems.Professor of Civil and Environmental Engineering
The research revealed that hyporheic exchange—a process in which surface water mixes with water in the riverbed—can trap lightweight microplastics that otherwise might be expected to float. The study is the first assessment of microplastic accumulation and residence times within freshwater systems, evaluating plastic pollution at its source and as it travels through the entire water stream.
“Most of what we know about plastics pollution we’ve learned from the oceans, because it’s very visible there,” says Aaron Packman, professor of civil and environmental engineering and one of the study’s senior authors. “Now, we know that small plastic particles, fragments, and fibers can be found nearly everywhere. However, we still don’t know what happens to the particles discharged from cities and wastewater.
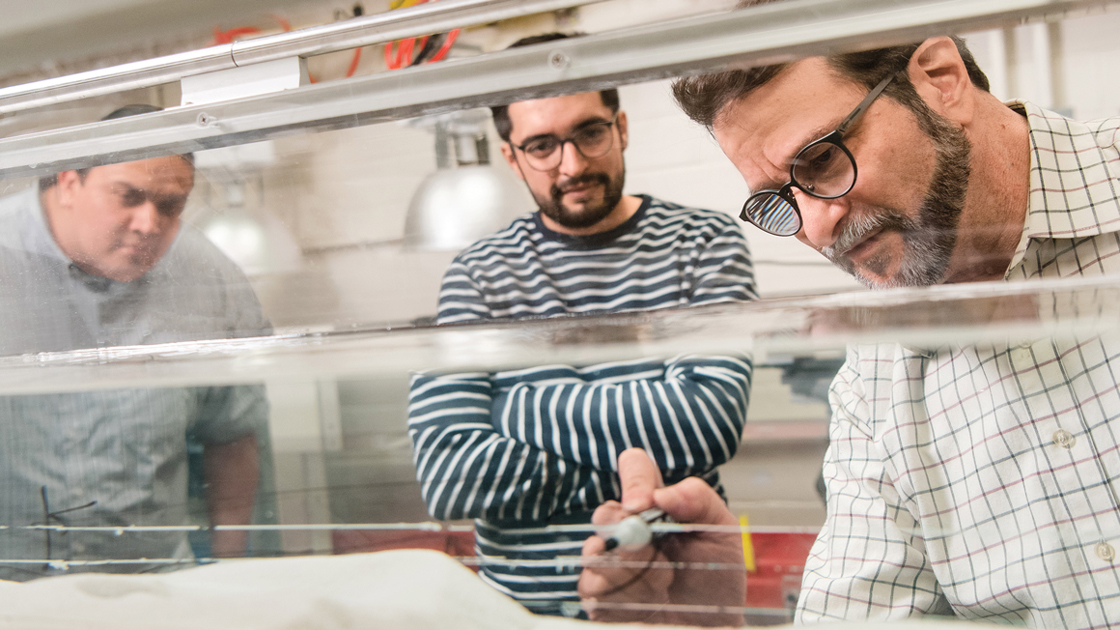
“Most of the work thus far has been to document where plastic particles can be found and how much is reaching the ocean. Our work shows that a lot of microplastics from urban wastewater end up depositing near a river’s source and take a long time to be transported downstream to oceans.”
To conduct the study, Packman, his former student Jennifer Drummond (now at the University of Birmingham), and their team developed a new model to simulate how individual particles enter freshwater systems, settle, and then later remobilize and redistribute. The model—which used global data on urban wastewater discharges and river flow conditions—is the first to include hyporheic exchange processes, which play a significant role in retaining microplastics within rivers.
Researchers found microplastic pollution resides the longest at headwaters, the source of a river or stream. In headwaters, microplastic particles moved at an average rate of one kilometer every five hours. But during low-flow conditions, this movement slowed to a creep—taking up to seven years to move the same distance. In these areas, organisms are more likely to ingest microplastics in the water, potentially degrading ecosystem health.
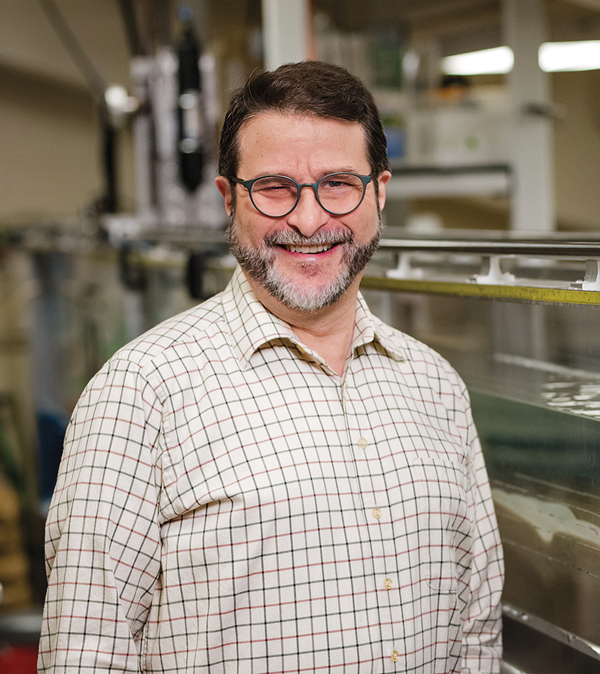
The residence time decreased as microplastics moved away from the headwaters, farther downstream. Residence times were shortest in large creeks that frequently flood.
Environmental scientists and engineers can use these findings to better assess and understand the long-term impacts of microplastic pollution on freshwater systems. “These deposited microplastics cause ecological damage, and the large amount of deposited particles means that it will take a very long time for all of them to be washed out of our freshwater ecosystems,” he says. “This information points us to consider whether we need solutions to remove these plastics to restore freshwater ecosystems.”
Relegating Dumps to History
Despite research and policy efforts, recycling initiatives have struggled with complex materials like tires and mattresses, leading to tons of unnecessary trash in dumps and landfills across the country.
This is a case of our looking at a class of materials that were considered hopeless in terms of recycling. We are using one- or twostep chemistry to transform them into recyclable material with full recovery of properties to see how that can really help address sustainability.Walter P. Murphy Professor of Chemical and Biological Engineering and Materials Science and Engineering
Soon, that could change. Thanks to efforts by Professor John Torkelson, such dumps could become little more than a bad memory. Torkelson is using simple chemistry to address longstanding barriers associated with recycling about a quarter of today’s plastics.
He and his team have developed new techniques to transform tires and other similar thermoset polymers into recyclable materials by changing their structure at the molecular level. The breakthrough research builds excitement in the sustainability field and could help mitigate fires, pollution, and the lost economic value associated with synthetic polymer waste.
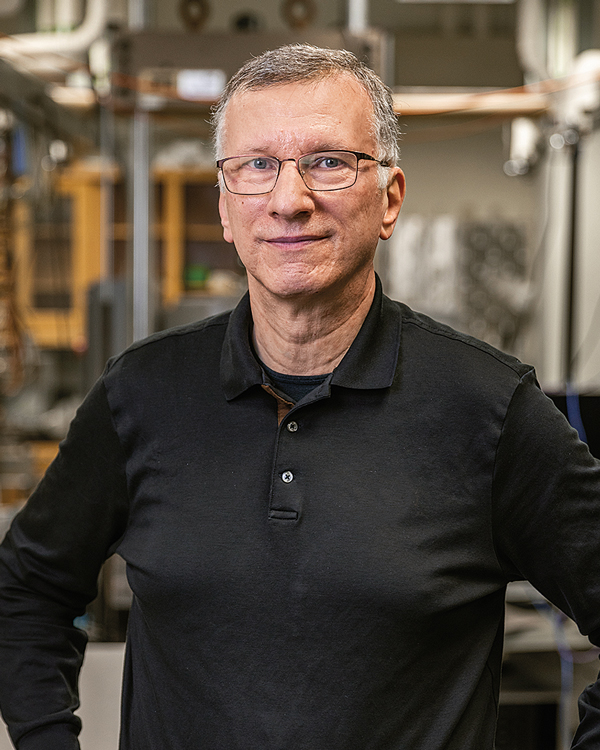
Synthetic polymers and plastics come from chemical reactions of monomers (molecules made up of single units). For example, ethylene makes polyethylene, which could be used to manufacture a milk jug. Termed thermoplastics, these materials can be recycled and melted down to create new products.
But tires and many other polymers constitute a class of materials called thermosets, made of long polymer chains that are permanently cross-linked. Cross-linked rubbers cannot be melted down and recycled into new products because of these permanent cross-links.
The Torkelson research group has found several ways to create a new type called dynamic covalent cross-links. These create robust cross-linking under conditions in which they are typically used, yet allow the materials to melt at a much hotter temperature.
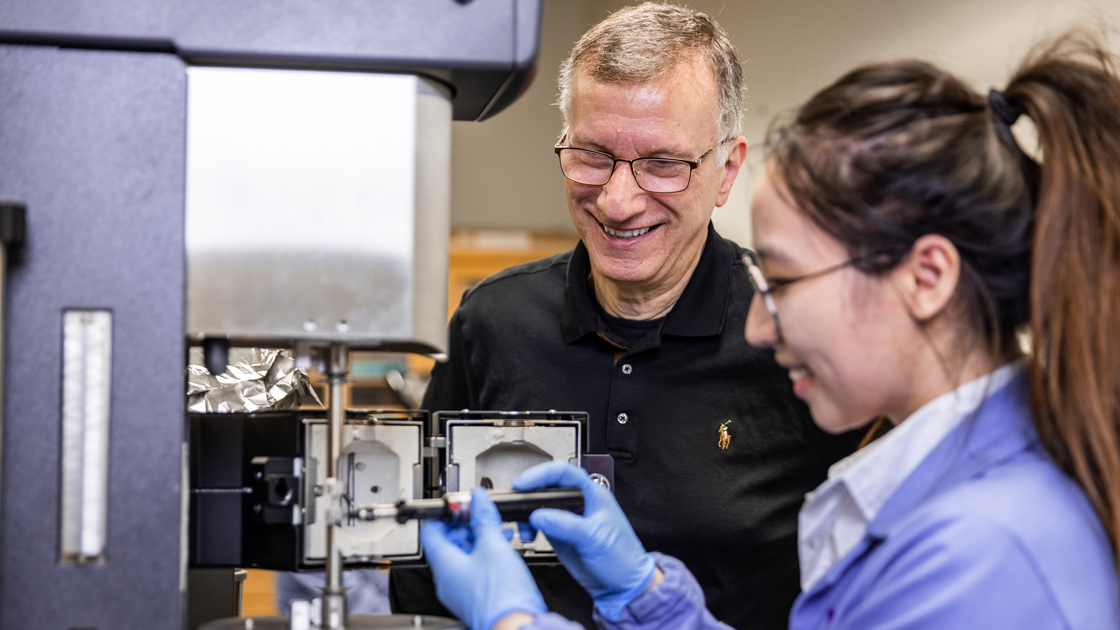
For example, a tire made of such material would melt at 280 degrees Fahrenheit, a temperature it would never reach under normal conditions of use. Then, when the recycled polymer is cooled again, the cross-links come back together just as strong, with the same properties as before.
“We’ve been able to effectively transform the thermosets into thermoplastics for recycling,” Torkelson says. “We can make cross-links that are just as robust as regular cross-links at use temperatures, but at high temperatures, they come apart temporarily.”
Researchers face an uphill battle when trying to address problems with entirely new materials, including trying to convince manufacturers to reinvent their literal and figurative wheels by adopting practices that may not balance out until years later. However, Torkelson’s solutions involve chemical reactions to existing materials, taking many steps—and years of development and implementation—out of the equation.
His work highlights success in synthesizing addition-type polymers, which are used to make car tires; step-growth-type polymers, with applications including foam mattresses and insulation; and sister cross-linked polymers, which can be made without toxic compounds, resulting in a highly viable material for recycling.
“My group has been dedicated to this work because it has so much potential,” Torkelson says. “We’re tackling problems that are important to saving the environment, while also doing well by the economy.”
Upcycling to Reduce Plastic Waste
Instead of renewing a commitment to recycling techniques that can only be used once on certain plastics, researchers have looked to other solutions to reduce plastic waste. Plastic upcycling, the process of efficiently deconstructing and rebuilding polymers— the essential building blocks of plastic—has become a major area of focus.
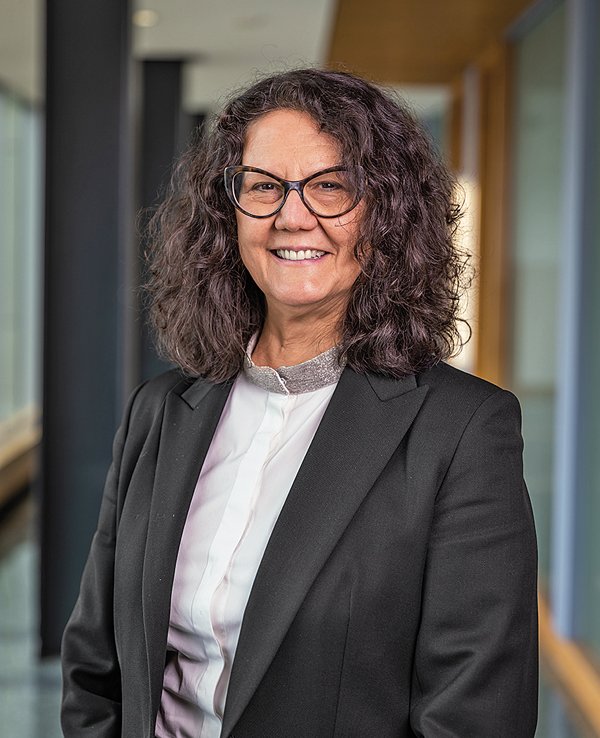
In contrast to recycling, where plastic is heated up, broken down, and then rebuilt into weaker, poorer quality plastics, upcycling breaks polymers down into their fundamental components, which sometimes allows them to become even sturdier plastics than they were before.
A team led by Monica Olvera de la Cruz, Lawyer Taylor Professor of Materials Science and Engineering and Chemistry, has provided the basis for a technique to enhance the effects of an enzyme that breaks down the plastic used to make soda bottles and inexpensive clothing—commercially termed PET—into its fundamental parts.
Olvera de la Cruz’s team hoped to create as green an upcycling process as possible—one that didn’t create pollutants but instead removed them. Using an enzyme that can be synthesized in a lab, the researchers developed a process that can be used repeatedly without using other solvents.
These are dangerous things that are bad for our health. We don’t need to make more. You can reuse the ones already here to make an equally good plastic—or better.Lawyer Taylor Professor of Materials Science and Engineering and Chemistry
In the study, the team designed a polymer and created the conditions needed to effectively protect the enzyme (called PETase), so that when the structure was heated, the PETase wouldn’t unravel and become ineffective. The polymer consists of a hydrophobic (water-repelling) backbone and highly specific concentrations of its three components, calculated by PhD student Curt Waltmann, to specifically interact with active sites on the enzyme.
“We found that if you put the complex of the polymer with the enzyme together, and near a plastic, and then you heat it up slightly, the enzyme was able to break it down into small, monomeric units,” Olvera de la Cruz says. “In addition to operating in an environment where it could clean microplastics, our method has protected against high temperature degradation.”
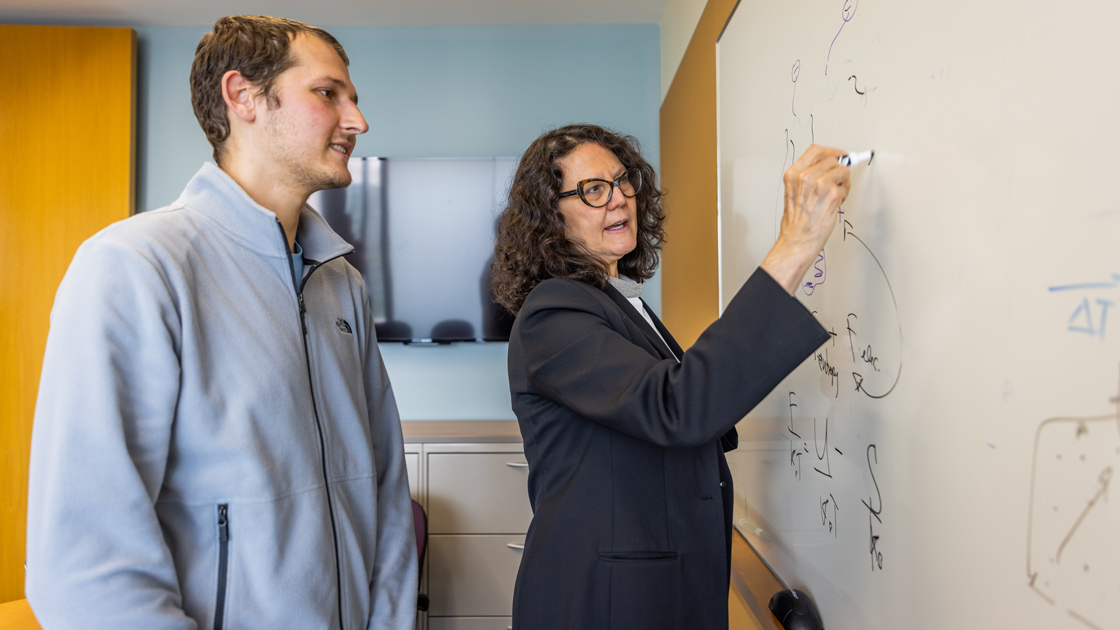
By finding a way to protect the enzyme from heat, the team opened many doors for the research community. For example, it could help engineers find solutions for removing microplastics from rivers and oceans.
The team, which includes John Torkelson and Danielle Tullman-Ercek, professor of chemical and biological engineering, has its sights set on encapsulating entire microplastics in the structure, then making an aggregate of microplastics with these enzymes.
“You can make a new polymer with the monomeric units,” Olvera de la Cruz says. “These are dangerous things that are bad for our health. We don’t need to make more. You can reuse the ones already here to make an equally good plastic—or better.”
Photography by Jason Brown and Matthew Allen