Making Plastics Production More Energy Efficient
New approach to chemical catalysis results in higher yields of propylene using less energy
Northwestern engineering researchers have demonstrated a new approach to chemical catalysis that results in high propylene yields using less energy. The findings could support more energy-efficient production processes for many plastics.
One of the highest volume chemical products, more than $100 billion worth of propylene is produced each year and used primarily to produce polypropylene for a variety of materials, from injection moldings in car parts to consumer products. Producing propylene is also energy intensive, requiring temperatures around 800 degrees Celsius to convert propane gas to propylene.
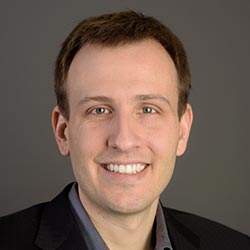
“The reaction works, but similar to when you turn on your gas grill to cook at home, you don't produce propylene, you just burn the propane,” said Justin Notestein, professor of chemical and biological engineering at the McCormick School of Engineering and a co-corresponding author on the research. “Instead of searching for the right catalyst, we deconstructed the oxidative dehydrogenation reaction down into two components — dehydrogenation and selective hydrogen combustion — and then designed a tandem material that does both reactions, in a particular order. This produced the highest yields of propylene ever reported.”
A paper titled “Tandem In2O3-Pt/Al2O3 Catalyst for Coupling of Propane Dehydrogenation to Selective H2 Combustion” was published March 19 in the journal Science. Peter Stair, professor of chemistry in the Weinberg College of Arts and Sciences, was the paper’s other co-corresponding author.
In the new approach, the researchers engineered two catalysts with nanoscale proximity: a platinum-based catalyst that selectively removes hydrogen from propane to make propylene, and an indium oxide-based catalyst that selectively burns the hydrogen, but not the propane or propylene.
“We found that the nanostructure really matters,” Notestein said. “Indium oxide on platinum works great. Platinum on indium oxide doesn't. Platinum physically combined with indium oxide doesn't. This nanostructure is able to separate and sequence the reactions, even though both catalysts can do both reactions. This organization is common in biology, but is very rare with human-made materials.”
The team’s tests produced notable improvements in propane yield to produce propylene. At 450 degrees Celsius, tests produced 30 percent yield from a single pass through the reactor, while ensuring that more than 75 percent of the carbon atoms in the propane went on to become propylene. By comparison, it is impossible to produce yields greater than 24 percent when heating propane in the absence of oxygen, and the required catalysts are often unstable.
“No one has ever demonstrated yields exceeding these thermodynamic limitations,” Notestein said. “From a utility point of view, our results are some of the first to really justify trying to do this reaction oxidatively, rather than just doing dehydrogenation.”
The system’s simple design could be further optimized by adjusting the reactor conditions and altering the two catalyst components. Current methods to produce higher yields require more complex and expensive engineering solutions.
“Since we rely on proven design-build-test cycles from engineering, there can be additional improvements,” said Notestein, director of the Center for Catalysis and Surface Science, part of the Institute for Sustainability and Energy at Northwestern. “These findings give us new compositions and rational strategies to try in the search for high-performing catalyst systems. This could especially benefit smaller chemical plants where energy consumption is very important and current engineering strategies may not be feasible.” He added the team’s approach reflects the larger efforts of the National Science Foundation’s Center for Innovative and Strategic Transformation of Alkane Resources (CISTAR), which funded the work.
The findings also could further improve the energy efficiency of manufacturing many plastics used in structural and materials applications. Plastic parts in cars, for example, make vehicles lighter in weight and more energy efficient, while polymer house wrap and siding is durable and helps keep homes warm and dry.
“Plastics, while much maligned, are essential to modern society, including efforts to make society more energy efficient,” Notestein said. “Making propylene, and materials like polypropylene, using this new approach could be much less energy intensive, which would be good news for everyone.”