Advancing Research through the Robot Design Studio
Students create two robots to advance work of mechanical engineering faculty
Northwestern Engineering students studying to be mechanical, computer, and electrical engineers – both undergraduate and graduate students – have all come together to build robots that advance research through the class MECH_ENG 495/ECE 495: Robot Design Studio.
The multidisciplinary course challenges students to take specifications for robot systems proposed by project partners and produce robust, working robot prototypes over the course of two quarters.
“If the students learn how to build a precision product that’s electromechanical in nature, working in a team environment, it’s just a win-win,” said co-instructor Ron Worth, adjunct lecturer in mechanical engineering at the McCormick School of Engineering.
This year, the second for this course, Robot Design Studio students first built their own motors, then worked in teams to create two different robots – projects that enhance research by Northwestern professors.
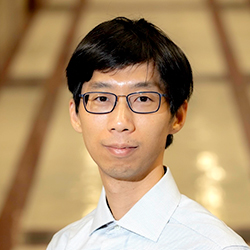
That project is Cablebot, a robot which is controlled by cables wound by precision-controlled motors. By controlling the cables, the payload in the middle can be moved over a large space – potentially as big as a football field.
This technology is similar to robot-controlled cameras used to film professional football games.
“It’s not a very intuitive problem to solve,” said Jordan Haskel, a master of science in robotics candidate who will graduate this month. “It’s a closed-loop robot. A lot of kinematics that we’re taught are for serial robots, so this is a different kind of problem.”
The second team is working with Kevin Lynch, chair and professor of mechanical engineering, to build an inexpensive high-precision robot with six degrees of freedom. The robot has six independently-actuated “legs” that drive a platform in three linear directions and three rotational directions. Lynch and his researchers plan to use this device, along with a force sensor, to test the multi-axis stiffness properties of experimental robot hand fingertips being developed in his lab.
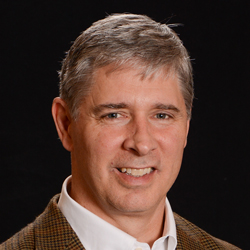
One of last year’s Robot Design Studio projects resulted in an experimental hopping robot. Dan Lynch, a mechanical engineering PhD student, helped to build the robot and is now using it for NASA-sponsored research investigating the design and control of legged robots to locomote on sandy, uneven terrain such as that found on Mars.
The class is grounded in exposure to industry leaders through guest lectures and design reviews where students receive feedback throughout the building process. The students also use industrial-grade parts to make the robots.
“Students get a sense of the industrial design process, including how to transform the wishes of the customer into testable engineering specifications,” said co-instructor Bill Hunt, a research engineer with Northwestern’s Neuroscience and Robotics Lab, who serves as the primary technical liaison for the class.
To reflect the industry experience, the class is often self-directed, but students are required to delegate tasks while building the robots.
“In real industry, you’re not doing it all. You have to learn to work with others toward the common goal,” Worth said. “A functioning robot requires the tight integration of software, mechanics, and electronics, and there’s no way to be successful without working together.”
The hands-on approach appeals to many students.
“I can take on a lot of coursework, but much of it is theory, and I don’t have a chance to apply it,” said John Girotto (’18), a graduating master’s candidate studying computer engineering. “Starting from taking apart a motor to actually scratch-building something to a high degree of precision and accuracy in this class has been quite an adventure.”