Creating Space on Mars
Northwestern Engineers bring deep-space construction to life as part of NASA's 3D-Printed Habitat Challenge.
The first humans to visit Mars are likely alive today, and NASA is planning to send one or more of them to the planet by 2040.
While exciting, the plan faces enormous logistical challenges. NASA scientists know that travel between Earth and the Red Planet takes nearly 10 months, and that room on board any spacecraft will be at a premium. What’s not known, however, is how the need for basic necessities will be met: What materials are available to create homes and other structures? What tools could be used? How will man-made structures
Though Mars is the planet most similar to Earth, crafting Martian living will require creative and efficient solutions. NASA put out a call for help, inviting thought leaders in industry and academia to the 3D-Printed Habitat Challenge to develop insights and create new technologies to manufacture a home on Mars using materials native to the planet. An interdisciplinary team led by Northwestern Engineers has answered with an award-winning design created with “Marscrete.”
Research Moves from Earth to Mars
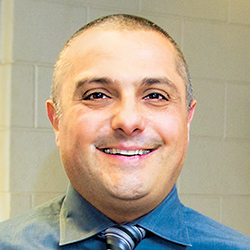
In 2014, just about the time NASA launched its challenge, Gianluca Cusatis, Northwestern Engineering associate professor of civil and environmental engineering, was exploring the potential of 3D printing — also known as additive manufacturing — for housing applications here on Earth.
He focused on construction, an industry that has battled stagnant productivity gains for two decades. While 3D-printing technology dates back to the 1980s, its use in construction was limited to creating small mechanical objects. Cusatis points out, however, “You don’t build small objects in civil engineering.
“We spent time learning what people were doing in the field of large-scale 3D printing,” he adds, having led Northwestern’s first workshop on the potential of large-scale 3D printing in 2017. The event brought together designers, architects, and engineers to explore how to print large structures — such as barracks in war zones or temporary housing in disaster areas —quickly and inexpensively with stronger, more durable, and more environmentally friendly materials.
"The thought of building on Mars captures imaginations in a new way. It makes people listen. It’s also an opportunity for us, as civil engineers, to showcase what we can do for our communities here at home.”
While testing these practical solutions for Earth-bound buildings in difficult places, the team learned of a chance to apply their research to a much more challenging location—Mars. “While we were exploring these opportunities, we learned of the NASA challenge, and thought it was a chance to build enthusiasm for large-scale 3D-printing research on campus,” Cusatis says.
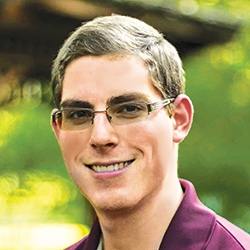
Cusatis turned to Matthew Troemner, an incoming
“You don’t often see such enthusiasm for civil engineering. We’ve always lived in houses and driven over bridges,” Cusatis says.
“We don’t view civil engineering innovation as disruptive as cell phone technology. But this project got everyone excited.”
"Martian 3Design" Takes Shape
The Northwestern team entered the 3D-Printed Habitat Challenge in January 2018 during the On-Site Habitat Competition, which tasked participants to create virtual renderings of a 1,000 square-foot house that could be built on Mars with a 3D printer and equipped to house four astronauts for up to one year.
"Our design initially started with one main entrance, but after we were given requirements from NASA to include a rover hatch, we decided to make the whole habitat symmetrical."
Called Martian 3Design, the team’s habitat combines sound structural engineering principles, building techniques that leverage Martian materials, and an intuitive floor plan that maximizes private and common spaces and resource efficiency. Features of the team’s design include:
- A 3D-printable inner spherical shell and outer parabolic dome that
protect the house against the harsh Martian climate - An interior layout that separates wet rooms (lab, kitchen, bathroom) from dry rooms (bedrooms, workstations) to limit the resources needed for construction
- Two hatch openings, located directly across from each other, which allow habitat units to easily connect to each other and foster community
“Our design initially started with one main entrance, but after we were given requirements from NASA to include a rover hatch, we decided to make the whole habitat symmetrical,” Troemner explains. “If we wanted to expand later on, not only would we have the rover hatch, which is required, but it could also accommodate a natural personnel hatch.”
The team also connected with Benton Johnson,
“SOM’s structural expertise informed a habitat design that let us 3D-print over an inflatable pressure vessel, a structure that would be strong enough to support its weight if there was a loss of pressure in the habitat,” Troemner says. “SOM also helped guide the overall shape and layout of our design.”
The ingenuity paid off. In July, NASA announced that the Northwestern team earned fifth place and a share of the $100,000 prize in the Level 1 Virtual Design Challenge. Martian 3Design, one of only 18 submissions from around the world chosen to be judged by NASA experts, placed higher than any other university.
“We were ecstatic to learn of our placement,” Troemner says. “The recognition was
Now, to Build It
Any design relies on physical tools to bring its potential to life. That’s why the team is focused on leveraging existing 3D-printing technology and Mars-local materials to make its habitat a reality. “We experimented to determine what combination of materials we could 3D-print consistently that also met the strength requirements defined by NASA,” Troemner says.
The team developed a building concrete composed entirely of materials found on Mars or recycled components of the
Guided by research on injection molding machines, the group designed a robotic arm-based 3D printer to construct its habitat. The six-axis system is not only more cost-efficient compared to other 3D printers, but it can be prototyped with a modified filament extruder to deposit the sulfur-based Martian concrete.
To operate the printer, the dry materials are loaded into the 3D printer’s extruder, where they are compressed and heated. The melted sulfur combines with the Mars simulant and is released as a paste, ready to be arranged into form by the robotic arm.
“The concrete hardens as strong as traditional casted concrete, but maintains properties that work well for 3D printing,” Troemner says. “Most 3D-printed concretes have to be premixed or pumped beforehand. This material is unique in that it can be loaded directly into the hopper.”
Meanwhile, Back on Earth
If selected, the Martian 3Design team will travel to the Caterpillar Peoria Proving Ground in Peoria, Illinois, in April for the Habitat Challenge’s culminating 3D-Printed Construction Competition. There, the team will use its 3D printer and Martian concrete to build a 1:3 scale model of the habitat envisioned in the Virtual Design Competition.
With NASA expected to announce the final competition’s top three finishers, who will share an $800,000 prize, in spring 2019, the team’s mission is nearly complete. But in many ways, according to Cusatis, the end is just the beginning. “Our hope has always been to build something that will live beyond the competition and afford us a chance to conduct more meaningful research in this new field,” he says.
While large-scale 3D printing is undoubtedly part of NASA’s plans to build its first human settlements on Mars, Cusatis believes these same technologies could jumpstart interest and innovation in a field that has long fought against it. “The thought of building on Mars captures imaginations in a new way. It makes people listen,” he adds. “It’s also an opportunity for us, as civil engineers, to showcase what we can do for our communities here at home.”
Martian 3Design's Outer Shell
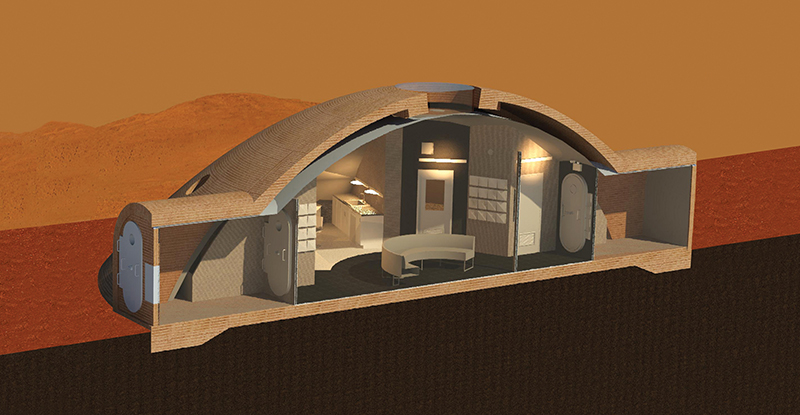
In designing the habitat’s outer shell shape, the team met with Donna Jurdy and Seth Stein, professors in Northwestern’s Department of Earth and Planetary Sciences, to brainstorm how 3D printing under Martian conditions would differ from Earth-based construction. The team’s igloo-style design takes into account the planet’s unique wind and gravity loads, as well as the potential for shifting sand dunes and meteorite impacts. “The outer shell acts as a kind of protective structure that is best suited for those loads,” says Matthew
Testing the 3D Printer
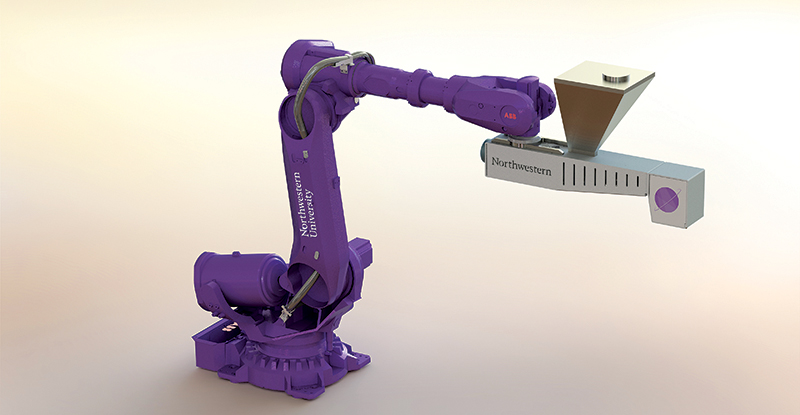
The team selected a multi-axis robotic arm from ABB Group to 3D-print
Inside the Habitat
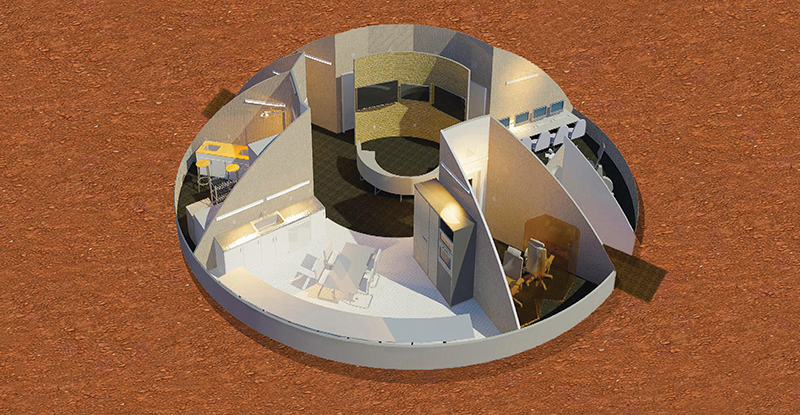
The team’s interior design for the 1,000-square-foot Martian habitat separates the space’s wet rooms, including the kitchen and lab, from dry rooms, like bedrooms and workstations. The arrangement consolidates plumbing and mechanical units to only one side of the habitat, eliminating excess materials running through the floors and walls.
The layout was inspired by the living quarters within the NASA-funded HI-SEAS (Hawaii Space Exploration Analog and Simulation) project, a Mars flight crew training simulator that sits on the Mauna Loa volcano approximately 8,200 feet above sea level on the Island of Hawaii
Mixing the Right "Marscrete"
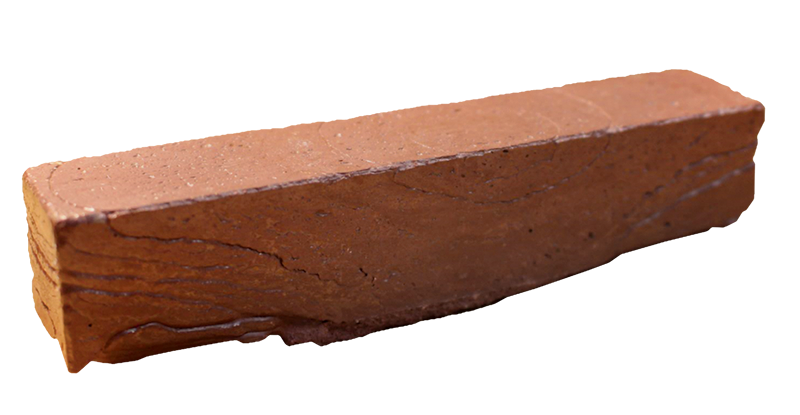