Researchers Nano-engineer New Aluminum Alloy
Lightweight and corrosion-resistant, aluminum alloys could provide an excellent alternative to steel or titanium — except for one problem. Most aluminum alloys are only good up to 200 degrees Celsius, which means they couldn't be used in high-temperature conditions, like in engines.
Now, professors at the McCormick School of Engineering and Applied Science at Northwestern University have created a new kind of aluminum alloy by engineering it at the nano level to give it high-strength and corrosion resistance to high temperatures. Their results were recently published in the journal Small.
David N. Seidman, Walter P. Murphy Professor of Materials Science and Engineering, and David C. Dunand, James N. and Margie M. Krebs Professor of Materials Science and Engineering, combined aluminum with lithium (which has a lower density than aluminum and makes the material more lightweight) and scandium — an exotic element that dramatically strengthens aluminum. They also added a bit of ytterbium, which also acts as a strengthener but is much cheaper than scandium.
But creating an alloy isn't just a matter of mixing the elements together — the researchers have a scientifically designed process of timed heating that naturally arranges the atoms into nano-particles with a new kind of structure — a core surrounded by two shells. The core is ytterbium-rich, while the first shell is rich in scandium and the second shell contains mostly lithium. This core/shell-shell structure has been achieved by chemists in liquid solutions but this is the first time it has been achieved by processing solely in the solid-state.
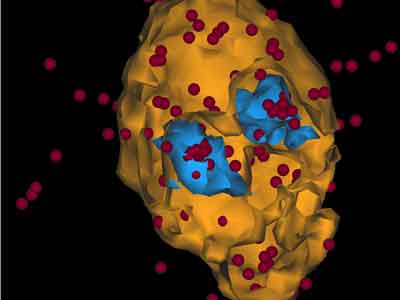
"We have shown that this process works in the solid state," Dunand said. "It shows we can make nano-particles that are complex and tuned to the properties we need. It could be applicable to a large number of alloys."
The researchers also found that some nano-particles had a structure they weren't expecting — a single particle with two cores and two outer shells, like a double-yolked egg. This is the first time this type of structure has been observed.
"That was the whipped cream on the cake," Seidman said. The professors said further research is needed on what such a structure could do for materials.
"It's the best when something unexpected happens," Dunand said. "The next step is to figure out whether this particle is superior to the single-core particles."
The two researchers have been collaborating on aluminum alloys for 10 years — utilizing different elements and measuring how the resulting material behaves at elevated temperatures. Dunand creates and tests the strength of the alloy, while Seidman characterizes it with atom probe tomography — an instrument that strips a material atom-by-atom to determine where atoms are located in three-dimensions and what they are made of, which yields a 3D reconstruction consisting of the atoms' positions and chemical identities. That is how the researchers knew the compositions of their core/shell-shell particles, despite their nanometric size.
While this research was supported by the Department of Energy, the two professors are also working with the Northwestern University Ford-Boeing Alliance on aluminum alloys that combine five elements — the most complicated alloys they've created yet, which could potentially replace steel in engines.
"All the basic science we have performed for 10 years has now reached the point where it's gathering interest in company world," Dunand said.
Next the researchers will undertake a systematic study to determine how different parameters affect their core/shell-shell structures and will continue testing the alloy for efficiency and tweaking the composition to make it optimal.
"We'd like to demonstrate that this approach can be used for many different alloys," Dunand said. "It's nanoengineering that could perhaps be a universal approach to creating new kinds of alloys that are tailored to specific needs."
The first author of the paper is Christian Monachon, an undergraduate student who was a visiting researcher from École Polytechnique Fédérale de Lausanne in Switzerland.