A New Strategy to 3D Print Miniature and Disposable Optical Microscopes
Cheng Sun developed the low-cost platform, which can be readily disseminated
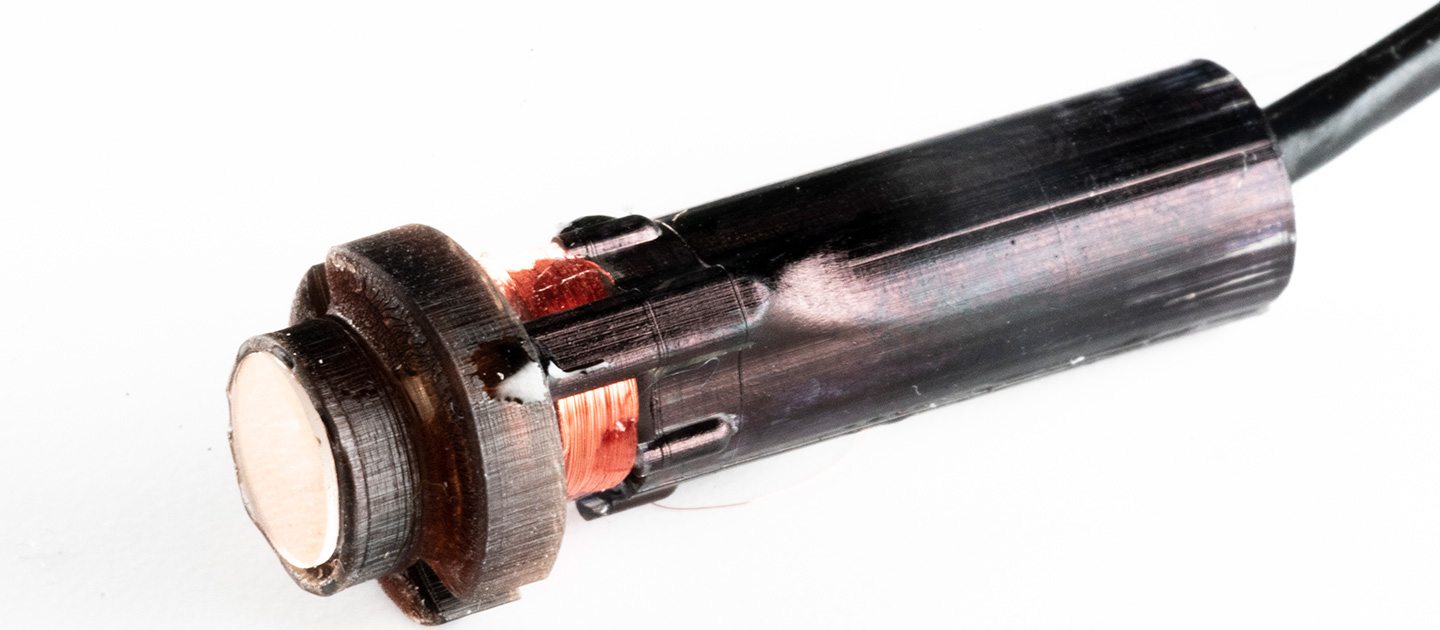
The demand for disposable miniature imaging platforms (DMIPs) is growing rapidly. Used for commercial, scientific, medical, and educational purposes, DMIPs have numerous applications but can be cost-prohibitive due to the sensitive and delicate nature of their components.
Northwestern Engineering’s Cheng Sun is working to make DMIPs more accessible for all.
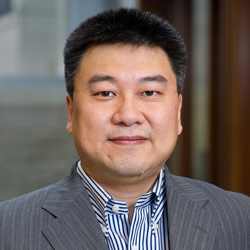
As reported in “3D Printing a Low-Cost Miniature Accommodating Optical Microscope” published open access on last month in the journal Advanced Materials and highlighted in Nature, Sun and his team developed a low-cost platform that can be readily disseminated to a broad community of potential users as an open-source project. To do this, Sun demonstrated the advantages of using 3D printing to enable the miniaturization of an optical imaging system, significantly reducing the component’s cost. 3D printing enabled the digitalization of the manufacture of optomechanical components, a smaller part-count, and the inclusion of passive alignment features.
The end result is a penny-sized component produced in 50 minutes, with each unit costing more than $4 less to manufacture than other methods.
“This work is motivated by the increasing demands in miniaturizing the optical imaging system,” said Sun, a professor of mechanical engineering at the McCormick School of Engineering. “Recently, multiple research groups, including us, have demonstrated the promising potential in 3D printing a millimeter-sized optical imaging lens. However, to create a functional imaging system, there are still unsolved challenges in precisely manufacturing and assembling the dimensionally compatible optomechanical components into a miniaturized optical imaging system.”
Our work represents a significant step forward from 3D printing optical lenses to a fully functional accommodating optical imaging system in a miniaturized form, and for much less cost to produce.
Cheng SunProfessor of Mechanical Engineering
Tackling this issue was Sun’s goal. He and his colleagues used an additive manufacturing strategy to unify traditionally discrete manufacturing processes for the ease of assembly and, ultimately, cost-savings. Using a miniaturized accommodating optical microscope with an outer diameter of 8.1 mm as a representative example, they demonstrated several distinct advantages of this approach:
- Reducing the system components to five 3D-printed and four off-the-shelf parts
- The passive alignment features throughout the 3D-printed part allows for easier assembly
- The digitized designs are readily customizable to accommodate demands in working distance and magnification, along with the choice of off-the-shelf polymer lenses
- The method significantly reduced the unit manufacturing cost to less than $4.
“By making use of its build-in accommodating capabilities, we implemented a focus stacking function by combining multiple images taken while axially translating the imaging lens, resulting in a specimen image with a greatly extended depth of field,” Sun said.
The findings build on a previous work from the researchers, where they demonstrated how to 3D-print millimeter-sized imaging lenses that could be used to create customized contact lenses for correcting distorted vision, or to turn iPhones into microscopes for disease diagnosis.
“Our work represents a significant step forward from 3D printing optical lenses to a fully functional accommodating optical imaging system in a miniaturized form, and for much less cost to produce,” Sun said.