Neural Network Predicts Plasticity of Materials
Deep learning methods model how materials deform under force
A new neural network structure developed at Northwestern Engineering can predict the plasticity of materials, considering a material’s microstructure better and faster than traditional approaches.
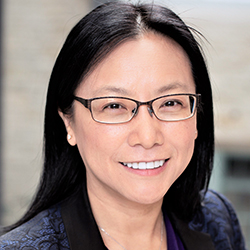
“As we develop more sophisticated materials, we need systematic ways to understand their complex behavior,” said Jian Cao, the Cardiss Collins Professor of Mechanical Engineering at Northwestern’s McCormick School of Engineering, who co-led the research. “Deep learning methods provide a way to do this with accuracy and speed to aid the optimization of design.”
The results were published December 16 in Proceedings of the National Academy of Sciences.
Material plasticity is difficult to model because it varies not just with the initial structure of a material, but also the history of deformation: If a material is deformed, that deformation can then affect other deformation later on. That knowledge is extremely important in industries like manufacturing, where a raw material is often formed into its final shape through several steps and processes.
Phenomenological mathematical models – models that describe the relationship of phenomena to each other – have historically been used to calculate plasticity, but such models are often based on certain restrictive theoretical assumptions and are therefore not sophisticated enough to model today’s complex, designed materials. While more sophisticated models exist (such as the crystal plasticity or multi-scale models), they are too slow and need hours or days of computational time on super-computers to solve a wide range of engineering problems.
To develop a more systematic way to model plasticity, Cao and her team used deep learning methods to create a neural network, a set of algorithms that can extract hidden relationships in data. The newly developed neural network architecture learns any material behavior under different force patterns and understands the plasticity of the material based on the material’s properties and its history of force.
“It’s purely data driven,” said Cao, who is also the director of the Northwestern Initiative for Manufacturing Science and Innovation. “The network can capture the evolution of the material without making assumptions on the nature of materials, which makes this approach widely applicable.”
The network allows engineers to design materials and manufacturing processes at the same time to truly enable an integrated system approach to optimization. Cao and her team hope to continue to test it with different material systems and integrate it into material design.
“It really achieves superior accuracy and speed for predicting material structures undergoing complex loading paths,” she said. “This could pave the way for physics-informed, data-driven modeling across many applications in physics and engineering.”
The lead author is Northwestern mechanical engineering PhD candidate Mojtaba Mozaffar. Other authors on the paper include Northwestern alumnus Miguel Bessa (co-corresponding author), assistant professor at Delft University of Technology; Northwestern alumnus Ramin Bostanabad, assistant professor at the University of California at Irvine; Wei Chen, Wilson-Cook Professor in Engineering Design and mechanical engineering at Northwestern; and Kornel Ehmann, professor of mechanical engineering at Northwestern.