New Model Explains How to Design Defect Tolerant Materials
A critical dimension indicates which material is more likely to fail
In the world of materials, the phrase “too big to fail” does not apply.
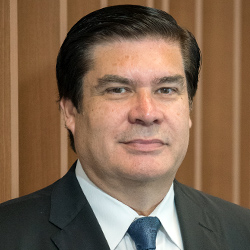
According to the well known “size effect,” defects tend to arise in materials as they are synthesized in the lab. As the defects accumulate, the material’s mechanical strength decreases. This means larger objects are more likely to fail than smaller objects, even if they’re made of the same material.
But size doesn’t impact strength in natural materials in the same way. Seashells and bones of varying sizes can grow without losing strength or toughness. Now a team of mechanical engineers at the McCormick School of Engineering has looked to examples in nature to better understand how these biomaterials avoid inherent defects as they grow.
Led by Horacio Espinosa, the James N. and Nancy J. Farley Professor in Manufacturing and Entrepreneurship, the research team formulated an advanced statistical model for staggered composite materials to explore how to introduce defect tolerance and suppress the size effects on material strength by controlling the microstructure of the material. Through rigorous mathematical derivations based on the model, they discovered a critical dimension “length scale” at which the material is more likely to fail.
“Our findings establish a deep understanding of the structure-property relationship in bio-inspired composites and demonstrate how certain composite materials can achieve size-independent material strength,” Espinosa said. “By factoring discontinuities into the composite architecture, in a controlled manner, staggered composites can achieve an incredible capability for defect tolerance.”
The research is described in the February issue of Acta Biomaterialia and was highlighted by Materials Today. Xiaoding Wei, a postdoctoral fellow in Espinosa’s lab, served as the paper’s first author.
“The critical length scale we found coincides with the fundamental link that had emerged in simulations for fiber-reinforced composites decades ago,” Wei said. “However, the understanding of its origin remained incomplete until we derived it through rigorous mathematical analysis.”
Espinosa and his team expect this research will provide valuable insights for the design of bio-inspired, high-performance composite materials. The model could potentially guide the material microstructure design to preserve strength and toughness as the material dimensions grow.
“We are planning to use our theoretical predictions to guide bio-inspired composite design, using modern synthesis techniques, such as 3-D printing to prototype novel high-performance materials,” Espinosa said.