Big Idea: A Softer Robot, Inspired by Muscles
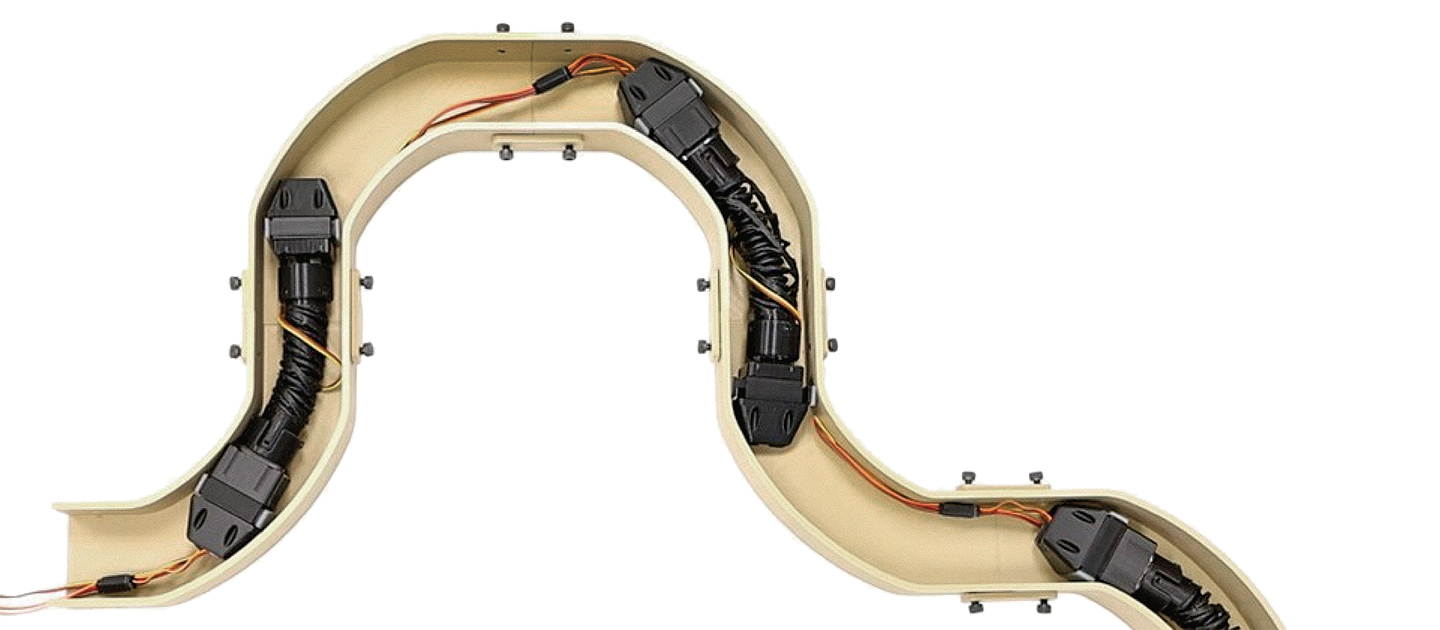
To create a safer, more practical robot, Professor Ryan Truby and his team developed a soft, flexible actuator that enables robots to move by expanding and contracting—just like a human muscle.
To demonstrate how the actuator works, the researchers used it to create a worm-like soft robot and an artificial bicep. In experiments, the soft robot navigated the tight, hairpin curves of a narrow, pipe-like environment. The bicep was able to lift a 500-gram weight 5,000 times in a row without failing.
Because the researchers 3D printed the body of the soft actuator using a common rubber, the robots cost about $3 in materials, excluding the small motor that drives the actuator’s shape change. That contrasts sharply with the cost of the typical rigid actuators, which can range from hundreds to thousands of dollars. The new actuator could be used to develop inexpensive, flexible robots that would be softer, safer, and more practical for many applications.
Truby is a member of Human AugmentatioN via Dexterity (HAND), a new US National Science Foundation Engineering Research Center led by Northwestern and dedicated to revolutionizing the ability of robots to amplify human labor.