Using Video Games to Teach Materials Science
Interdisciplinary project distills technical materials science research concepts into fun web-based games
Students in Professor David Dunand’s research group are playing video games on the clock. But they aren’t slacking or procrastinating — they’re translating technical research into fun and educational web-based games.
Through the Structural Metallic Materials Group, Dunand, professor of materials science and engineering at Northwestern Engineering, investigates the mechanical metallurgy of advanced metallic alloys, composites, foams, and scaffolds. Through novel processing techniques and characterization of microstructure properties, Dunand and his team develop light- and/or heat-resistant metals for energy and transportation applications as well as biomedical technology.
They also prioritize making this research more tangible and relevant to the public by connecting methods like freeze-casting or 3D ink extrusion printing to more familiar reference points through interactive games.
“Games are the most natural and the first way we learn new things,” Dunand said. “Playing is learning.”
Game development takes off
Dunand and his team first explored the potential of using video games as an educational outreach tool in 2016 with the SpaceICE (Interface Convective Effects) CubeSat Mission project. A partnership with the University of Illinois Urbana-Champaign (UIUC) and Bradley University supported by NASA’s Office of Education, the nanosatellite project was designed to investigate freeze-casting in the microgravity environment of low Earth orbit.
Freeze-casting, or ice-templating, is a low-cost, directional solidification technique that is used to fabricate a range of material foams — including ceramics, metals, polymers, and composites — with aligned pore structures that can be manipulated depending on the specific solvent and freezing process, allowing the foam to act as a reactor, filter, or heat sink.
The Northwestern team, led by Kristen Scotti (PhD ’23), and the Bradley University Interactive Media Department developed a 2D Tetris-style game called L.U.M.P.I Space Adventure, demonstrating the concept of freeze-casting as players build layers with different shapes around vertically rising icicles. Designed primarily for youth ages six to eight, players “earn money” to build and enhance CubeSats by stacking pieces and minimizing gaps, representing the porosity. The game won a bronze medal in 2018 at the game-based learning Serious Play Conference.
Exploring new dimensions
Building on the fundamental knowledge of freeze-cast processing and microstructure relationships that the team gained during the SpaceICE mission, the Dunand Research Group is currently investigating methods — such as adding an alloying element — to stabilize freeze-cast iron foams and increase their usable lifetime.
Sam Pennell, a PhD student in materials science and engineering, is the lead on a project funded through August 2024 by the National Science Foundation’s (NSF) Division of Civil, Mechanical, and Manufacturing Innovation (CMMI). Pennell and his team — which also includes postdoctoral scholar Ming Chen and Ryan Asali, a rising fourth-year undergraduate student in materials science and engineering at the McCormick School of Engineering — are applying the freeze-casting technique to iron oxides to generate stable, relatively inexpensive structures for application in the advanced clean energy materials sector.
Pennell aims to improve the performance and optimal efficiency of rechargeable oxide batteries, which connect a fuel cell to a finite supply of hydrogen that uses iron to cycle between hydrogen and water.
“We tested a lot of different iron-plus-X-element combinations. By alloying iron with other metals, we've been able to improve its degradation-resistance,” Pennell said. “We've also learned a lot about how the cyclical process of iron oxidizing to iron oxide and then reducing back to iron, which is helpful research for this and for other fields like steel manufacturing.”
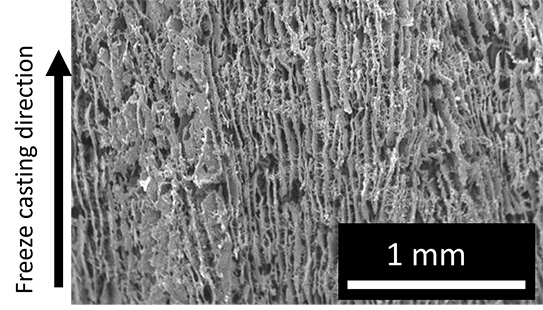
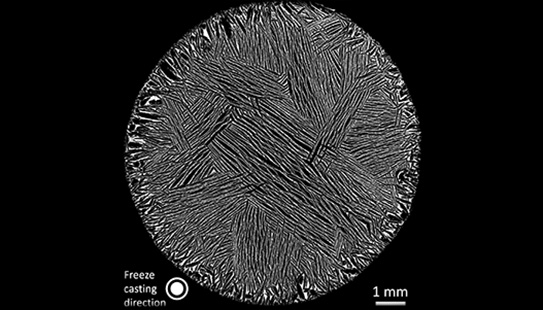
As the freeze-casting research progressed, Pennell and Dunand also wanted to improve on the concept of the L.U.M.P.I. Space Adventure and launch a new, more exciting version of the Tetris-style game.
There was just one problem — they aren’t game developers.
Pennell posted a message on the Northwestern Software and Game Development Group Discord server and immediately received a response from Isaac Brown, a rising third-year undergraduate student pursuing dual bachelor’s degrees in computer science at Northwestern Engineering and in trumpet performance at Northwestern’s Bienen School of Music.
Brown is interested in low-level systems software development, or the back-end, hidden code that runs applications such as connecting to Wi-Fi or opening files from a USB flash drive. A self-taught game developer, Brown has been developing games as a side hobby on the Unity platform for several years. He grew up immersed in implicit learning experiences, first encouraged by his father to explore Scratch, the block-based visual programming language developed by MIT, and then playing educational games in elementary and middle school on websites like Cool Math Games.
“The game format is a really fantastic way to communicate the general concepts without being overly complex or overpowering,” Brown said. “It's great that Professor Dunand is trying that on a higher level and that I'm getting to participate. It's a good endeavor.”
Brown, Dunand, Pennell, and John Misiaszek, a PhD student in materials science and engineering, determined in their first meeting that the core innovation of the new game would be a 3D format.
“Isaac was the lead and main driving force of the actual game development. He's very talented,” Pennell said. “Our role was to give him a general idea of what we wanted, and then playtest it and give him feedback.”
After an iterative development process over this past winter and spring quarter, Brown released TetrIce in June, an arcade-style game inspired by freeze-casting in which players arrange falling blocks in a 3D grid while avoiding growing ice pillars. Unlike the original 2D Tetris with one axis of rotation, TetrIce features three axes of rotation and three axes of movement.
The biggest challenge Brown faced was designing a set of controls that would be intuitive within the complex 3D structure of the game.
“I needed at least six different controls just for the movement of the blocks,” Brown said. “And then, we needed controls to rotate the whole rectangular prism board as well so the player’s view would not be obscured.”
To assist with visualizing the grid when it becomes crowded with blocks, players can toggle a transparency setting so gaps in the board are highlighted.
In addition to building the programming and graphics, Brown also created the game’s music using the digital audio workstation Ableton. He used a virtual synthesizer to create tracks of different instruments, layered those tracks, then adjusted the pitches and volumes for each instrument.
Brown also recorded and produced the sound effects.
“That was fun getting to do a little bit of Foley art,” Brown said.
Though he was initially apprehensive about balancing the game development with the research project, Pennell is thrilled with the outcome.
“This was a fun break from the regular research — completely different than what we normally do,” Pennell said. “And it's really a blast working with Isaac to develop this game and show off freeze-casting as a technique.”
The iron oxides redox cycling project is also proceeding successfully.
“The project has actually been doing really well,” Pennell said. “We’ve been quite successful so far on developing ways to prolong the lifespan of these energy storage materials.”
Pennell is writing up the team’s past year of results and plans to collaborate with a fuel cell lab to test the freeze-cast structures in a practical setting and evaluate their performance generating electricity. He anticipates completing his PhD program next year and aims to begin a career in the energy, storage, and conversion industry.
“This is the first time I've led a project and I've definitely learned so much about how to organize it, how to set up experiments, and how to train new people coming on to the project, which is new for me, and something that I really like doing,” Pennell said.
A slice of life
Demonstrating the concepts of additive manufacturing and tomography, Brown also developed a spatial awareness puzzle video game called 3D Think for a project involving Misiaszek and PhD students Ya-Chu Hsu and Dingchang Zhang on 3D-printed metallic alloy scaffolds. The research is supported by the NSF Division of Materials Research.
Using the direct-ink write extrusion method, Hsu and Zhang create high-strength microlattices from extruded inks (blends of oxide and hydride powders), while Misiaszek aims to design longer-lasting, orthopedic implants using commercially pure titanium inks. Misiaszek has a personal connection to his research. After he broke his leg in a 2017 skiing accident, he received a titanium implant.
“It’s certainly a motivating factor, because I’m experiencing what it’s like right now,” Misiaszek said. “I want to make reliable implants that last a long time.”
By introducing microporosity in the struts using sodium chloride space holders and thus reducing the stiffness of the implant, Misiaszek is trying to counter two common problems with structural, permanent orthopedic implants: stress shielding, which is a reduction in bone density caused by the disproportionate load-bearing of the implant, and aseptic loosening – the body’s inflammatory response to debris particles generated by the wear of the implant.
Misiaszek generated titanium scaffolds to span two transverse processes on the spinal column and then handed them off to Nick Sather, associate director for translational research and technology transfer with the Simpson Querrey Institute for BioNanotechnology (SQI), who infiltrated the scaffolds with bioactive materials that helps bone cells grow. Next, residents in the lab of Erin Hsu, assistant director of SQI and a research associate professor of orthopaedic surgery at Northwestern University Feinberg School of Medicine, implanted the scaffolds into rat models and monitored them for eight weeks.
To assess the porosity of the titanium as well as assess the bone growth inside the scaffolds, Misiaszek conducted tomographic analysis on the spines using the synchrotron at Argonne National Laboratory’s Advanced Photon Source in collaboration with Stuart Stock, a research professor of cell and developmental biology at Feinberg.
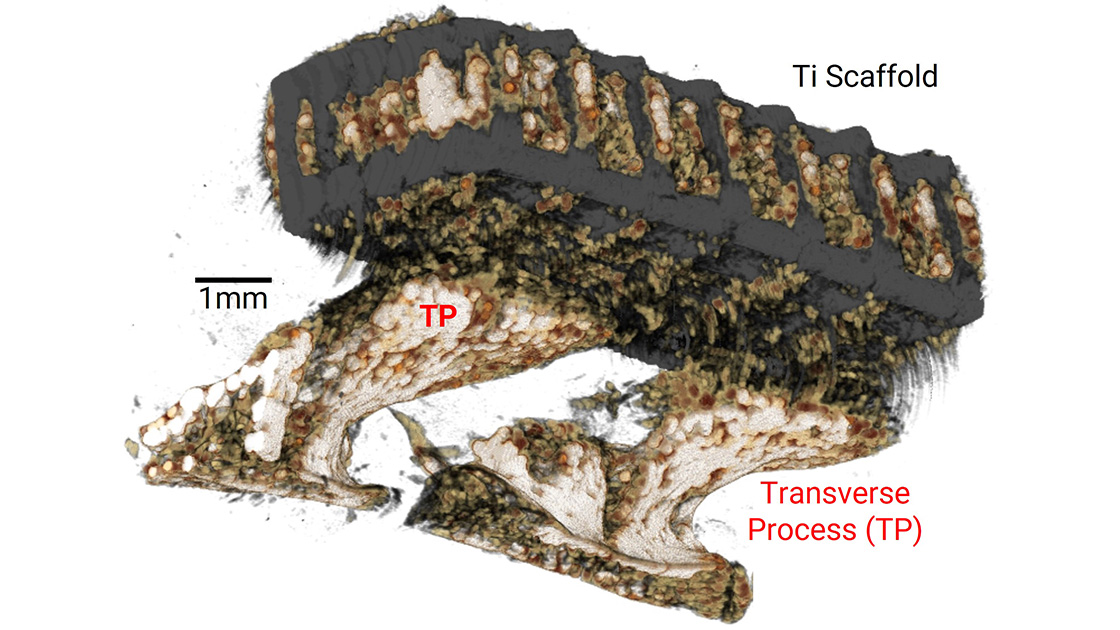
Tomography generates cross-sectional images of an object via a penetrating wave such as X-ray or ultrasound, allowing the microstructure of an object to be analyzed nondestructively.
Inspired by his experience using 3D printing software as an undergraduate student, Misiaszek formulated the idea for the 3D Think game. Players are presented with 3D models of familiar objects — including a LEGO figure, lantern, bug, and chair — and must select the corresponding cross-section as quickly as possible.
Dunand had originally proposed a different premise, which involved 3D printing robots by moving the extruder head.
“John came up with the 3D Think concept and I thought it was so superior that we completely shifted gears,” Dunand said. “Students very often have great ideas and when they have a better idea, then we follow it. Because I don't have expertise in games, our roles are somewhat reversed. I'm the one who is a novice to the video game area and the students were in their element, so they were truly in charge.”
Brown developed a novel slice algorithm to generate the cross-sections using 3D models he accessed through Ultimaker’s Thingiverse, a repository for open-source, community-generated digital designs.
“I realized I could manipulate the 3D model data to generate random cross sections on the fly as the game is being played so that it would in theory be infinitely playable, or at least playable more times than if we had just manually picked out a few cross sections,” Brown said. “There was a chance that it wouldn't work out. I didn't really have any concrete ideas of how to do that, but I figured it was probably possible, and it would be cool enough that it would be worth giving it a shot.”
Brown and Misiaszek connected every few weeks to discuss how the project was going, evaluate design improvements, and where to go next.
“Isaac was fantastic to work with. He can take our ideas and translate them very well into code,” Misiaszek said. “These fundamental techniques are very specialized and it's hard to communicate this to a general audience in a palatable way, so one of the objectives of this video game was to do exactly that.”
Working on 3D Think planted a seed for Misiaszek about science communication.
“When people think about science, it's like a black box. It can be very hard to peer in because you need so much background to understand anything,” Misiaszek said. “Video games like these have really been motivational because it's a way to communicate why science is important and why we need to continue doing science. I definitely plan to do more outreach like this in the future.”
Game building continues
Dunand is so enthused by L.U.M.P.I. Space Adventure, TetrIce, and 3D Think, he incorporated game development into two recent funding proposals.
“I had a great time seeing the games evolve, being able to work with the students on how to modify them and make them better,” Dunand said. “I must say, it’s a great bit of fun for me to be part of that.”
Dunand, Brown, and Jie Qi, a postdoctoral scholar in materials science and engineering, have begun discussions around a “find the difference” game related to an aluminum alloy project supported by the US Department of Energy Advanced Manufacturing Office in partnership with Boeing and Wisconsin-based foundry Eck Industries Inc.
The game will underscore the brain’s ability to rapidly identify differences and similarities in complex microstructures and will also showcase hundreds of maze-like micrograph images from the lab.
“The microstructures are inherently beautiful, like brain coral,” Dunand said. “When you see it, you're just fascinated by the intricate pattern hiding in metals and alloys at micron-scale.”
Dunand also proposed a videogame as part of a pending NSF proposal that would illustrate the concepts of chemical reduction and reaction kinetics.
“NSF and the other grantees are putting strong emphasis on the outreach. I feel I need to really to do my very best, not just in the science which I do for them, but also to push the boundary on outreach,” Dunand said. “I’ve done quite a bit of work at the interface between art and science and so that has allowed me to be more receptive to the idea of exploring the gaming aspects of technology. A big part of my family background is more literary and artistic and I'm kind of the black sheep having done science, but this merges both.”