By Water, by Land, by Air
Northwestern Engineers tackle energy efficiency issues from multiple fronts
Professor Yip-Wah Chung knows energy efficiency—or perhaps more accurately inefficiency—by the numbers. If asked, he can rattle them off the top of his head.
- 35%: The average energy efficiency of a US fossil fuel-burning power plant. (US Energy Information Administration Monthly Energy Review)
- 27%: The world average energy efficiency of a coal-burning power plant. (World Coal Association)
- 15–20%: The energy efficiency of the average automobile. (Holmberg, K.; Andersson, P.; Nylund, N.-O.; Mäkelä, K.; Erdemir, A. “Global energy consumption due to friction in trucks and buses.” Tribology International 78 (October 2014): 94–114.)
- 3,000: The fuel a Boeing 747 burns every hour—much of which is wasted. (The Boeing Company; number represents the fuel burn rate at cruise speeds (550 mph))
The numbers go on and on. “It’s mind numbing,” says Chung, a professor of materials science and engineering in Northwestern’s McCormick School of Engineering, referring to the dismal energy efficiency numbers. “It’s impossible to get to 100 percent efficiency, but there’s a lot of room for improvement to use less energy to accomplish the same amount of work. Every fraction of a percent counts.”
Chung is one member of an extended and growing team of Northwestern engineers avidly working to make industries, transportation, and individual households more energy efficient. They are tackling the issue from all sides: land, water, and air.
What Is Energy Efficiency?
Energy efficiency is the percentage of energy put into a machine and consumed in useful work, rather than wasted as heat or other byproducts.
Of the fuel put into a car, for example, only about 20 percent actually propels the vehicle down the road. The rest is wasted as heat exhaust or used to counter friction and air drag.
“If we can solve the problem of energy inefficiency, we can change the world,” Chung says. “I honestly believe that.” There are some PRACTICAL BENEFITS for increased energy efficiency in how people use equipment and lead their lives.
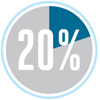
For starters, it would:
- Lower energy costs
- Reduce pollution and greenhouse gas emissions
- Mitigate overall energy needs
- Increase national security by decreasing reliance on imports
Although renewable energies such as wind, solar, and battery power can address cost and pollution issues, Northwestern Engineering experts also believe in the importance of getting the most out of fossil fuels. “There’s already a huge legacy and huge infrastructure in place for fossil fuels,” says David Dunand, professor of materials science and engineering.
“We need to look for more efficient ways to burn fossil fuels and to improve solar and wind technologies. It’s not one or the other. It’s both.”

Materializing Solutions for Power Plants
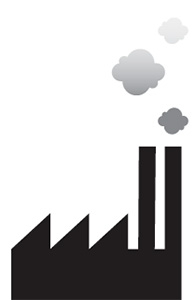
They produce electricity by setting off a long chain of events that starts by burning fuel to produce steam. That steam then drives a turbine, which powers a generator to ultimately make electricity. Increasing the energy efficiency of power plants could dramatically decrease the cost of power production and reduce the volume of carbon emissions.
David Dunand and David Seidman, Walter P. Murphy Professor of Materials Science and Engineering, are working toward those goals from a materials perspective. The backbone of their work is Carnot’s theorem, based on the second law of thermodynamics. A simple formula, the theorem outlines the maximum amount of electricity (useful work) that can be extracted from a unit of fuel. The efficiency depends solely on the difference in temperature between the hot and cold components involved in the process. For power plants, it all comes down to the steam. The hotter the steam, the more electricity is produced.
“Essentially, the hotter you can get the temperature to burn the fuel, the more electricity you can extract,” Dunand explains. “The cold part is just the surrounding air, so you can’t do much about that. What you can do, though, is get the hot part hotter.”
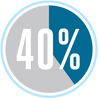
Though Carnot’s formula is a straightforward statement, the simplicity ends there. The challenge that researchers face lies in finding materials for the turbines that can function in extreme heat. For the past 100 years, researchers have toiled to create alloys that can withstand higher and higher temperatures. Nickel-based and iron-based superalloys, which initially emerged quickly as the two leading materials, have nearly reached their potential.
“These alloys have been tweaked and tweaked,” Dunand says. “The current nickel-based superalloys have 15 elements in them. Researchers keep adding more elements—a pinch of this, a whisper of that. There’s not much more we can do; we’re starting to plateau.”
Researchers, including Dunand and Seidman, have pinpointed cobalt as nickel’s successor. Next to nickel on the periodic table of elements, cobalt shares several of its sister element’s best assets. Both, for example, resist corrosion. And though both exhibit great strength at high temperatures, cobalt does one better.
“THAT'S A BIG DEAL,” Dunand says. “If you get an improvement of one degree per year, you’re happy. So 50 degrees would be tremendous. You’d save billions of dollars in fuel and reduce megatons of carbon emissions.”
Supported by the Center for Hierarchical Materials Design and the National Institute of Standards and Technology, Dunand and Seidman are manipulating the microstructure of a cobalt-based superalloy to make it less likely to deform at high temperatures yet remain resistant to oxidation. Their existing superalloy contains 10 elements, which Dunand likened to a human taking 10 different medications.
“Each element has its own side effects,” he says. But he believes this new material could increase power plants’ energy efficiency by 1 or 2 percent to save billions of dollars and gigatons of emitted carbon. What’s better, the turbines can be simply dropped into existing power plants to work with current infrastructure.
Scientifically, we know where we’re going, and what’s possible. We’re moving much faster than researchers moved when developing nickel-based alloys. The payoffs will be huge.
Superalloys Aloft
Dunand and Seidman’s superalloys don’t just apply to turbines in power plants. Jet engine turbines could also be constructed from the Northwestern duo’s materials. Like power plants, jet engine turbines are commonly made of nickel-based superalloys. But existing commercial airplanes have already maxed out the temperature that these materials can withstand.
Nickel melts at 1,450°C, but an airplane’s combustion chamber reaches 1,400°C. A ceramic coating on the turbine blades creates a thermal barrier that drops the melting temperature by 150°C. Engineers hollow out the blades and fill them with coolants, which further reduces the blade’s melting temperature. Replacing current turbines with Dunand and Seidman’s cobalt-based superalloys might enable engineers to forgo the hollow cooling chambers altogether, increasing the energy efficiency across the turbine’s lifecycle.
"Then you could have a much cheaper blade because you wouldn’t have to create all those intricate channels,” Dunand says. “You could make the blade lighter, thinner. Lighter infrastructure would allow you to have more passengers. There’s more than one way to cash in on that increased performance.”
Allies and Alloys
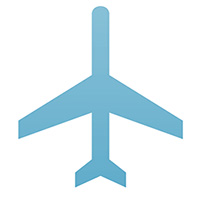
Printing Plane Parts
When it comes to increasing airplanes’ energy efficiency, Eric Masanet’s solution comes in three dimensions.
Masanet, an associate professor of mechanical engineering and chemical and biological engineering, discovered that by manufacturing metal aircraft parts with 3D printing, airlines could save a significant amount of fuel, materials, and other resources.
Masanet and his team used aircraft industry data to complete a case study of the lifecycle environmental effects of using 3D printing for select aircraft parts, a technique already being explored by the industry. The team concluded that 3D printing the lighter and higher performance parts could significantly reduce manufacturing waste and the weight of the airplane, saving fuel and money and reducing carbon emissions.
The currently used conventional manufacturingmethods tend to be inefficient and wasteful. The manufacturing process for a one kilogram bracket for an airplane, for example, might require 10 kilograms of raw material. From an engineering design perspective, that final bracket might still contain much more metal than required for the job. 3D printing, on the other hand, not only requires far fewer raw material inputs, but can also produce parts that minimize weight through better design.
“We have suboptimal designs because we’re limited by conventional manufacturing,” Masanet says. “When you can make something in layer-by-layer fashion, those constraints diminish.”
Ground Control
While the production of electricity accounts for 40 percent of US energy consumption, transportation comes in a close second at 30 percent, a number that continues to grow. Because energy consumption increases as the population grows and living standards rise, the level of fuel waste is likely to surge as well.
“Energy consumption per person becomes higher and higher as lifestyle improves. Everybody used to walk. Now everybody drives. We can’t tell people to go back to walking or not to drive. We have to develop technology solutions.”
Although many solutions can gouge the wallet, such as replacing fuel-burning cars with electric cars, Professors Wang, Yip-Wah Chung, and Tobin Marks have developed a simpler alternative to improve the efficiency of everyday vehicles. The team has created new lubricant additives that can significantly reduce friction and wear on modern automotive engine components without poisoning the catalytic converter. For the average car, about 15 percent of fuel consumption is spent overcoming friction. Reducing friction not only enhances fuel efficiency but also lengthens the engine’s life.
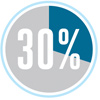
The team recently developed a new lubricant additive group called Cyclens, which can reduce friction by up to 70 percent and wear by up to 90 percent compared to conventional lubricant counterparts.
Cyclens additives are made of organic molecules with nitrogen centers. The multiple nitrogen centers enable the lubricant to bind to a surface, an important factor that keeps the lubricant in place between surfaces.
“It’s a drop-in replacement, so you don’t need to do anything except add this chemical to the oil,” Chung says. “And then bang! The friction drops.”
Wang and Chung have also partnered with Jiaxing Huang, professor of materials science and engineering, to explore a more unusual lubricant additive: crumpled graphene balls. About six years ago, Huang discovered crumpled graphene balls—a novel type of ultrafine particles that resemble crumpled paper. He made the particles by drying tiny water droplets with graphene-based sheets inside.
“Capillary force generated by the evaporation of water crumples the sheets into miniaturized paper balls,” Huang said. “Just like how we crumple a piece of paper with our hands.”
In a series of tests, a base oil modified only with crumpled graphene balls outperformed fully formulated commercial oil, both in terms of reducing friction and the degree of wear on steel surfaces. Because of their unique shape, crumpled graphene balls self disperse without needing surfactants that are attracted to oil. With their pointy surfaces, they simply can’t make close contact with other graphene balls. Even when squeezed together, they easily separate again when disturbed.
Water from Thin Air
Gathering, treating, and transporting water is one of the most energy-expensive tasks that humans undertake. Delivering water to remote, dry regions usually means constructing miles of pipelines, travelling long distances by truck or ocean tanker, or desalinating seawater.
All of those methods can be very costly and energy intensive and come with varying environmental and social impacts. Using locally available water is, of course, more cost effective and energy efficient, but some regions have no readily apparent local sources of water. Even though it’s not visible to those regions’ residents, the solution could be literally in front of their noses.
“Where is water?” asks Neelesh Patankar, professor of mechanical engineering. “It’s underground in wells and on land in oceans, rivers, and lakes. But there is also water vapor in the air. The question is: Are we leaving money on the table there?” And that’s exactly what Patankar is trying to answer.
He and Kyoo Chul Park, assistant professor of mechanical engineering, use surface engineering to harvest water from the atmosphere. Their decentralized solution could allow people in all regions to collect their own water without the need for long-distance transportation. And because water vapor is high quality, this water source requires less filtering—another energy efficiency.
The harvesting method manipulates water’s phase behavior—the temperatures at which it boils, condenses, and freezes. Most people believe that water must be boiled to vaporize. “Actually, forming vapor without boiling water is not unheard of,” Patankar explains. “If I put a drop of water on the table, it’s going to evaporate eventually. Our idea was to reverse this trick by making surfaces on which vapor would like to condense as dew and easily roll-off.”
Inspired by the hydrophobic surfaces of lotus leaves—micro- and nanoscopic bumps on the leaves cause water to bead up and roll off—Patankar and Park developed surfaces on which water drops can easily slide off. Park found a combination of surface chemistry and roughness that causes water vapor to condense easily as dew and roll-off quickly for collection. People can then harvest the dew for drinking water.
Patankar and Park imagine that people in water-scarce regions could someday have coolers inside their homes to harvest atmospheric water for drinking. The process would also solve other problems by dehumidifying houses to prevent mold formation, protect electronics in humid regions, and improve the quality of life.
“Our work is about investing in a sustainable future,” Park says. “We want to help alleviate suffering in the developing world by contributing to the next generation of technologies that address water scarcity.”
Living an Efficient Life
Yip-Wah Chung walks the talk about energy efficiency. When he moved into his new house, he immediately put his knowledge into action. By making a few simple changes, he slashed both his energy waste and his power bill.
“There are so many things we—not as scientists and engineers, but as private citizens—can do to make an impact,” he says. “To me, that’s empowerment.”
Here are Chung’s top tips for leading more efficient lives:
In the house:
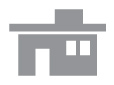
- Turn off lights when leaving the room.
- Set the thermostat so HVAC systems run less frequently while sleeping or away from home.
- Switch from regular light bulbs to LED bulbs.
“LEDs seem expensive, but they are a one-time investment,” Chung says. “They last for years, so over time, they cover their own costs. If you don’t expect to live in the same place for the life of the bulb, take it with you when you move.” - Improve home insulation to prevent heat and cool air from escaping.
- Replace appliances with ENERGY STAR certified models.
In the car:

- Remove junk from inside the car; excess weight reduces fuel economy.
- Change oil every six months to minimize friction and wear.
- Anticipate traffic changes to avoid sudden braking or accelerating.
- On highways, drive the speed limit.
- “At highway speeds, aerodynamic drag is the main source of energy loss,” Chung says. “Drag increases as the square of the vehicle speed, which means that by driving 10 percent faster—60 miles per hour instead of 55—the drag and gas consumption increase by about 20 percent.”
- Choose a hybrid or electric model.
Coming Next: Self-cleaning Energy?
Not only does the lotus leaf repel water, it’s also self-cleaning. When water beads up and rolls off the leaves, it takes dirt with it. Professor Kyoo Chul Park wants to use his energy efficient surface coatings on solar cells to create the same effect.
“Within a couple months of installation, solar cells get dirty, and their energy efficiency decreases by 40 percent,” Park says. “It’s important to maintain a high quality of transparency.” Park believes that a functional coating to make solar cells self-cleaning could increase energy efficiency.
“Our work is about investing in a sustainable future. We want to help alleviate suffering in the developing world by contributing to the next generation of technologies that address water scarcity.”