20 Years Later: Cobots Co-opt Assembly Lines
Northwestern team collaborated with GM to create a new type of robot
When humans work together, they typically share the load. Through cooperation, one person lifts one side of a heavy couch and another person lifts the other side. They talk through motions and feel each other push and pull.
But 20 years ago, people could not work with robots in a similarly natural way. That began to change in 1995 when Northwestern Engineering’s J. Edward Colgate and Michael Peshkin undertook a research project on collaborative robots.
“The whole emphasis in the field at the time was robot autonomy — not cooperation,” said Peshkin, professor of mechanical engineering and now the Bette and Neison Harris Professor in Teaching Excellence. “Robots didn’t have any mechanisms for cooperation with a person.”
“Robots were sensory impaired,” added Colgate, professor of mechanical engineering and the Allen K. and Johnnie Cordell Breed Senior Professor in Design. “They knew nothing about the world around them, so they couldn’t do much with people without the risk of hurting them.”
The idea to make a robot to cooperate with people was born on the factory floor of a pickup truck assembly plant in Fort Wayne, Indiana.
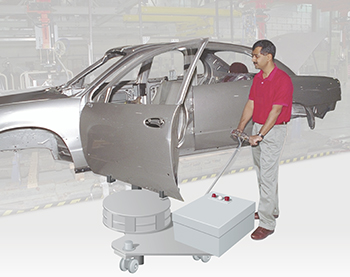
While there were robots on the assembly line, they operated strictly behind fences, keeping people at a distance.
“We anticipated that the GM workers would shun us because they would think we were trying to automate more jobs,” Peshkin said. “But they were welcoming. They quickly understood that machines could offer physical help.”
“The workers have a great deal of nuance, skill, and pride in their work,” Colgate said. “We aimed to understand their needs by observing, trying their jobs ourselves, listening to their concerns, and using engineering thinking.”
Joined by Prasad Akella, a lead engineer at GM, Colgate and Peshkin decided to design a safe robot that could work closely humans and make life easier. They aimed to provide what they termed “constraint surfaces”: computer-controlled pathways that support and guide a payload into its desire location smoothly while still under the immediate physical control of the worker.
Colgate and Peshkin initially called their invention a “programmable constraint machine.” They offered a $50 reward to the lab member who could come up with a friendlier name. Post-doctoral fellow Brent Gillespie, who is now an associate professor at the University of Michigan, pitched “cobots” and took the prize. The word quickly caught on and was even listed as a “word of tomorrow” by The Wall Street Journal in its millennium edition on January 1, 2000.
To ensure safety, Colgate and Peshkin’s first cobots did not have a power source of their own. Instead, a human co-worker provided the force needed to move a payload, and the cobot contributed a computer-controlled guidance pathway. If a payload started to go in the wrong direction, the cobot smoothly guided it back onto the path. Subsequent cobots provided motive force as well, but in limited amounts.
“We thought about putting powerful motors into the cobots,” Colgate said, “but decided it was too dangerous.”
Colgate and Peshkin turned their invention into a company called Cobotics, which was eventually purchased by Stanley Works. Today, the term “cobot” has re-emerged as a generic term for all collaborative robots. Other companies have even started producing robots to work with people, calling them “intelligent assist devices.”
Whatever the name, cobots, intelligent assist devices, and collaborative robots are now in use at GM and other automakers as well as finding their way into other industries.