Supercharged. Better Batteries Ahead
From anode to the cathode — and everything in between — Northwestern Engineering researchers are finding ways to make cheaper, lighter batteries that work better and last longer.
What’s driving — or more accurately, not driving — widespread consumer adoption of all-electric automobiles?
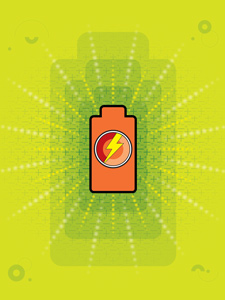
These cars certainly make great sense environmentally. With zero tailpipe emissions, these cars could put a major dent into the amount of carbon dioxide in the atmosphere, reduce fossil fuel reliance, and help slow climate change. But that’s only if people actually drive them. So far, they don’t, thanks to decades-old battery technology that limits their range and offers few options for charging.
That could change fast. A team of Northwestern Engineers is working to design better batteries — batteries that are cheaper, lighter, and with much greater capacity than today’s models — that could make all-electric cars more feasible for average citizens, affecting the environment in an enormously positive way.
The implications of their work extend far beyond automobiles, of course, to include virtually all battery-dependent devices and gadgets. As Northwestern Engineering’s Christopher Wolverton, professor of materials science and engineering, notes, “We all want a laptop that will survive an entire transatlantic flight without dying. But improving automotive technology: that’s the Holy Grail.”
“Transportation is one of the biggest energy-consumption sectors,” says Harold Kung, the Walter P. Murphy Professor of Chemical and Biological Engineering. “The obvious solution is to replace fossil fuels with renewable energy. But right now, the renewable generation of electricity is still more expensive than conventional methods. We have to develop a source of electricity that poses no drawbacks.”
THE HIGH PRICE OF POWER
In an all-electric car, the battery comes in as the single most expensive component. In Tesla’s flagship Model S, for example, the battery pack alone costs approximately $30,000, or 42 percent, of the total cost. Such a significant price tag catapults electric cars to a higher price point than most consumers can afford. And price isn’t even the most troubling problem.
Many drivers suffer from “range anxiety,” the fear of running out of power before they can get to the next recharging station. The fear is not unfounded as such stations are still few and far between. A typical electric car can only travel a couple hundred miles before reaching the end of its charge, when it must be plugged in to recharge for several hours. That range is much shorter than the 300 to 400 miles that a conventionally powered car can cover on one tank of gas.
“You can’t use an electric car the same way as you use a normal automobile, which you can to drive across country,” says Mark Hersam, the Walter P. Murphy Professor of Materials Science and Engineering. “Or, at least you have to manage it differently, and people aren’t used to that. We need to build batteries that give drivers an experience similar to what they’re used to — or better.”
HOW BATTERIES WORK
Ever since Sony released it in 1997, the lithium-ion battery has set the gold standard for battery technology. Compared to earlier ancestors, the lithium-ion model is the lowest density battery with the greatest energy-to-weight ratio.
This popular iteration has three components: the anode, the cathode, and the electrolyte. The anode, typically made of graphite, holds the negative charge. The cathode, a combination of lithium, a conductive metal, and an oxide, holds the positive charge. The electrolyte, held within a solid polymer composite, serves simply as a transport medium for the lithium ions to move between the anode and cathode.
When a battery is in use, lithium ions travel from the anode to the cathode. When the battery is charged, the ions move back to the anode, where they are stored.
ANODE RESEARCH
Coming up with the best materials, tools, and designs for building better batteries requires exhaustive research involving materials science and chemical engineering. One of the consistent quests is to make a battery that can store more energy in the anode. Researchers discovered that anodes made with silicon rather than the traditional graphite can hold more lithium, but silicon expands and contracts during the charging and discharging process. These size fluctuations can cause the anode to crack and ultimately the battery to fail.
“If the coating is a tight shell, which is usually easier to make, it will crack when the silicon particles expand,” Huang says. “The crumpled graphene has a lot of wrinkles that simply smooth out when the silicon expands and then wrinkle back up when it contracts.”
Professor Kung solved this problem by sandwiching silicon between graphene sheets, capturing all the benefits of silicon, along with padding to accommodate volume changes during use. The resulting anode could be a game-changer in the battery world: a battery that charges 10 times faster with 10 times greater charge than existing batteries.
This work, which could pave the way for better batteries for smartphones, laptops, and automobiles, has spawned a Northwestern spin-off company, SiNode Systems, to commercialize the research. Kung predicts his battery could hit the market within three years.
“If the coating is a tight shell, which is usually easier to make, it will crack when the silicon particles expand,” Huang says. “The crumpled graphene has a lot of wrinkles that simply smooth out when the silicon expands and then wrinkle back up when it contracts.”
Jiaxing Huang, associate professor of materials science and engineering, is also addressing the same problem with graphene — but with a twist. Huang developed a crumpled graphene “pocket” that can also protect the silicon nanoparticles as they change in size.
CATHODE RESEARCH
Most battery research focuses on the cathode side: twice as many scholarly articles examine the cathode over the anode, and Northwestern Engineers fit solidly within this trend. “In some sense, the cathode is where the action is because it controls the voltage,” Wolverton says. “It has the lithium in it when the battery is discharged. When you plug in your phone and charge it, lithium is being pulled out of the cathode.”
“The cathode really requires completely new materials that, at this point, are unknown,” Hersam says.
“The cathode limits the overall performance of the battery more than the anode,” adds Mark Hersam. “You have to make a major improvement to the anode side to see any difference in performance. Even a small change to the cathode side can make a significant difference overall.”
Researchers are still searching for materials that will give the cathode significantly higher capacity. The most common battery — the kind found in smart phones — uses lithium and cobalt, but cobalt is toxic, expensive, has a limited capacity for lithium, and is capable of overheating.
“The cathode really requires completely new materials that, at this point, are unknown,” Hersam says.
AN INTERDISCIPLINARY SEARCH
Six years ago, the US Department of Energy established an Energy Frontier Research Center (EFRC) dedicated to advancing lithium-ion batteries, with particular focus on the cathode. Called the Center for Electrochemical Energy Science (CEES), it’s a collaborative effort among Northwestern, Argonne National Laboratory, and University of Illinois at Urbana-Champaign. Along with Hersam, Northwestern members include Michael Bedzyk, Scott Barnett, Vinayak Dravid, Tobin Marks, and Wolverton.
“The battery problem is so big that we need many different perspectives with a highly interdisciplinary approach,” says Hersam, Northwestern’s principal investigator on the project. “I think the Northwestern effort would be successful if self-contained, but it’s amplified by our partners.”
“The battery problem is so big that we need many different perspectives with a highly interdisciplinary approach,” says Hersam, Northwestern’s principal investigator on the project. “I think the Northwestern effort would be successful if self-contained, but it’s amplified by our partners.”
The search for a new cathode material has been challenging, but one candidate stands out: lithium-manganese-oxide, or LMO, which has many desirable attributes. It can be operated at a high voltage, it’s cheaper than cobalt, and it’s environmentally friendly. But as the battery charges and discharges, the manganese leeches into the electrolyte, significantly decreasing the battery’s lifetime.
A CEES-based team, including Hersam, Dravid, and Wolverton, developed a single-layer graphene coating to prevent the manganese from dissolving. When applied to the cathode, the coating acts as a filter, allowing the lithium ions to travel to the anode and back while keeping the manganese in place. Highly conductive graphene also enables the battery to charge faster. After careful testing, the team found that the coating improves the LMO battery’s lifetime by a factor of 10.
“Because graphene is so stable chemically, the electrolyte no longer makes direct contact with the LMO, minimizing the chance for chemistry to occur at that interface,” Hersam says. “That may also contribute to improved performance.”
To further understand this promising material, the team plans to examine it with an X-ray scattering technique at Argonne’s Advanced Photon Source (APS). The high-energy, ultra-bright X-ray beams can reveal information about LMO’s crystal structure, chemical composition, and physical properties.
“X-ray scattering can essentially allow us to see inside of the battery,” says Scott Barnett, professor of materials science and engineering. “But for the technique to work, we need a very thin, completely flat layer.”
To produce this material for X-ray analysis, Barnett employs two different methods. One technique uses a laser to strike the material, which vaporizes it and then deposits it as a thin film onto a substrate. The other technique uses energized ions to collide with the material, which ejects particles onto a substrate, forming a thin film.
While promising, LMO is not the only material with potential as a cathode material. Wolverton’s group performs high-throughput computations to find new materials for various applications, including batteries. He has used this technique to search for coatings other than graphene for LMO as well as for completely different alternatives to LMO.
“Some metal oxides are known coating materials and offer promising real-world improvements,” Wolverton says. “But is it the best we’ve found in our computations? No. We have other materials we think are better, but we haven’t tested them yet.”
The Dow Chemical Company has tasked Wolverton with finding ways to fix problems in a lithium-rich material, for which it holds the intellectual property rights. The material stores much more lithium than existing batteries, but with one major drawback: the battery’s voltage fades every time it is charged or discharged, which means performance declines with use over time. Wolverton’s group is designing a material that coats the cathode to prevent this problem. Using computation, he can explore why certain coating materials work and others do not.
“Once we’ve done a large number of these high-throughput computations and have a database of possibilities, we can quickly scan through our options,” he says. “That gives us lots of new combinations to try.”
As the lithium-rich battery degrades, hydrofluoric acid forms as a byproduct. According to Wolverton’s hypothesis, this acid attacks the cathode, dissolving the metal. His team is designing a coating that will sacrificially react with the acid. “It will essentially scavenge all of the hydrofluoric acid that comes near the cathode and react with it, leaving the cathode to still do its work in the battery,” he says.
LOOKING BEYOND CATHODES AND ANODES
Sometimes battery research has nothing to do with the cathode or the anode but, instead, addresses something else entirely. Here are a few examples of these outside-the-box efforts to build a better battery.
STRETCHABLE BATTERIES
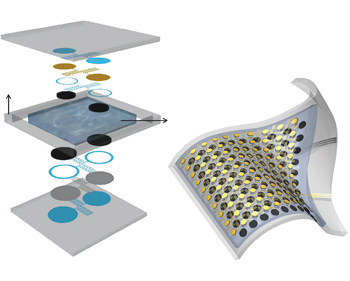
The device embeds tiny, lithium-based batteries into a paper-thin silicon sheet. The batteries are connected by a framework of coiled conductive wires, which uncoil when the battery is stretched. The device can work for eight to nine hours before it needs recharging, which can be done wirelessly.
Because Huang’s stretchable electronic device is completely independent of a cord and electrical outlet, the places where it could be used are almost limitless. This includes implanting it inside the human body, where it could power the monitoring of anything from brain waves to heart activity, succeeding where flat, rigid batteries would fail.
ION HIGHWAY SYSTEMS
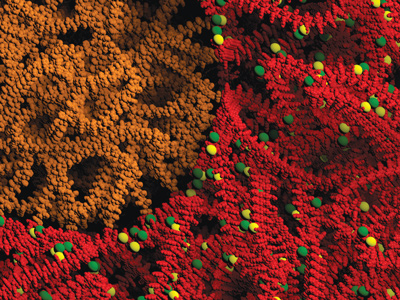
Block copolymers innately have nanochannels through which ions can travel, but the charges themselves manipulate the shape of the channels. To use the material in batteries, researchers must find a way to control the shape of the nanochannels to enable the charge to move efficiently.
Olvera de la Cruz and her team discovered that ions and counter-ions found in the nanochannels attract each other to form a salt. These salts cluster into miniature crystals, which exert a force on the nano-channels, changing the channels’ structures. This understanding makes it possible to predict and even design a “highway system” through which ions are transported, maximizing the power of the battery.
SWEAT EQUITY
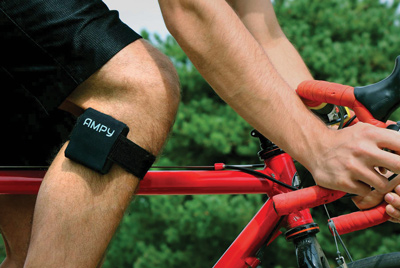
The device works with a patent-pending, proprietary inductor technology that generates electricity to charge an internal battery. It can store a week’s worth of energy, which can then be used to charge any device with a USB port. A 30-minute run, for example, can give a smartphone a three-hour charge or a smartwatch a 24-hour charge.
SAVING SILICON
In manufacturing wafers for computer chips, a chainsaw slices through a bulk piece of silicon, generating silicon dusts that are swept up and thrown away. That means about half of that expensive material is wasted in the process.
For two decades, researchers have tried different ways to recycle the wasted silicon. Some have suggested melting the powder down to make more computer chips; others have recommended adding it to concrete. Most of these ideas either require expensive refining processes to make the powder useful, or convert the silicon powder into less valuable materials
Northwestern’s Jiaxing Huang recently reported a new idea: Use the powder for batteries. Collaborating with his former visiting scholar Hee Dong Jang in Korea, he found that the silicon powder, once extracted, can be used as-is in the anode without further refining.
“Battery applications are much more tolerant of impurities than making chips,” Huang says. “Now you can take waste from one industry and repurpose it as a much value-added material for another industry.”